In many scenes of today's business and life, customized acrylic rectangle boxes play an extremely important role. Whether it is used for displaying exquisite goods, packaging precious gifts, or storing special items, its transparent, beautiful, and strong characteristics are favored. However, in the process of ordering these custom boxes, many people often fall into mistakes due to lack of experience or negligence, which leads to the final product being unsatisfactory and may even suffer financial losses.
This article will discuss in detail the common mistakes to avoid when ordering custom acrylic rectangular boxes, providing you with a comprehensive guide to help you complete your order successfully and achieve satisfactory results.
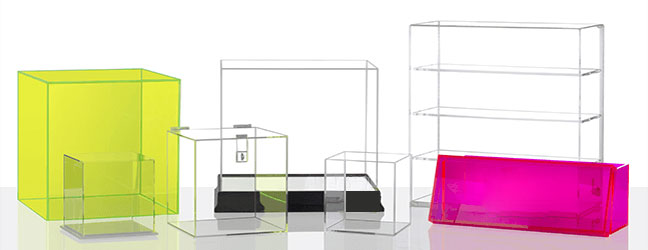
1. The Error of Unclear Requirements
Size ambiguity:
Accurate sizing is essential for customizing the box.
Failure to accurately measure or communicate the length, width, and height dimensions of the desired box to the supplier can lead to several problems. For example, if the size of the box is too small, the items that are intended to be placed in it will not be able to be loaded smoothly, which will not only affect the protection of the items but also may require re-customization of the box, resulting in a waste of time and money. Conversely, if the size of the box is too large, it will appear loose when used for display or packaging, affecting the overall aesthetics and professionalism.
For example, when a jewelry store orders acrylic rectangle boxes for display, because it does not accurately measure the size of the jewelry and consider the space limit of the display frame, the received boxes either cannot fit the jewelry or are not arranged neatly on the display frame, which seriously affects the display effect of the store.
Improper selection of thickness:
Acrylic sheets are available in a variety of thicknesses, and the purpose of the box determines the appropriate thickness required. If the specific purpose of the box is not clear to determine the thickness at will, it may lead to an imbalance between quality and cost.
For a box that is only used for the display of light items or simple packaging, if you choose too thick an acrylic sheet, it will increase unnecessary material costs and make the budget overspend. For boxes that need to carry heavier items, such as storage boxes for tools or models, if the thickness is too thin, it cannot provide sufficient strength and stability, which is easy to causes deformation or damage to the box, affecting the safety of storage.
For example, when a crafting studio ordered rectangular acrylic boxes for storing small handicrafts, it chose too thin plates without considering the weight of the handicrafts and the possible extrusion of the boxes. As a result, the boxes broke during transportation and many of the handicrafts were damaged.

Ignoring color and opacity details:
Color and transparency are important components of the appearance of acrylic rectangle boxes, which can greatly affect the display effect of products and the communication of brand image. If you do not fully consider the brand image, display environment, and item characteristics at the time of ordering, and choose color and transparency at will, the final product may be far from the expected.
For example, when a high-end fashion brand customized rectangular acrylic boxes for packaging its new perfume, instead of choosing transparent and high-grade acrylic materials that matched the brand image, it mistakenly chose darker and less transparent materials, which made the packaging look cheap and failed to highlight the high-end quality of the perfume. Thus, it affects the overall image and sales effect of the product in the market.

Missing special design and functional requirements:
In order to meet specific use scenarios and improve the practicality of the box, some special designs and functions are often required, such as carving brand logos, adding built-in partitions, and adopting special sealing methods. If you forget to mention these special designs in the ordering process, it may cause a large increase in the cost of later modifications, and may even fail to meet the actual use function.
For example, when ordering acrylic rectangle boxes for packaging headphones, an electronics manufacturer did not require the addition of partitions to fix the headphones and their accessories. As a result, the headphones and accessories collided and wound each other during transportation, which not only affected the appearance of the product but also caused product failures and brought adverse experiences to customers.
2. Acrylic Rectangle Box Manufacturer Selection Error
Choosing the right manufacturer is a key link to ensure the quality and on-time delivery of customized acrylic rectangle boxes, but it is also prone to many errors in this regard.
Based on price alone:
While price is one of the important factors to consider in the ordering process, it is by no means the only determining factor.
Some buyers rush to sign a contract with a manufacturer just because the offer is low, ignoring key factors such as product quality, production capacity, and after-sales service. The result of doing so is often to receive inferior quality products, such as scratches on the surface of the acrylic sheet, irregular cutting, and unstable assembly. Moreover, low-priced manufacturers may cause delivery delays due to poor equipment, insufficient personnel skills, or poor management, seriously affecting their own business plans or project progress.
For example, in order to reduce costs, an e-commerce enterprise chooses an acrylic box manufacturer with a very low price. As a result, there are a lot of quality problems in the received boxes, and many customers return the goods due to damaged packaging after receiving them, which not only loses a lot of freight and commodity value but also damages the reputation of the enterprise.
Insufficient research on manufacturer reputation:
The manufacturer's reputation is an important guarantee of its ability to deliver products on time and with quality. If we do not check information such as word of mouth, customer reviews, and business history when selecting a manufacturer, we are likely to cooperate with a manufacturer with a bad reputation. Such a manufacturer may commit fraud, such as false advertising, shoddy goods, or refuse to take responsibility when quality problems occur, leaving the purchaser in trouble.
For example, a gift shop ordered a batch of acrylic rectangle boxes without understanding the reputation of the supplier. As a result, the boxes received were seriously inconsistent with the samples, but the manufacturer refused to refund or exchange the goods. The gift shop had to bear the loss by itself, resulting in tight funds and affecting subsequent business activities.
Ignoring the manufacturer's capacity assessment:
The production capacity of the manufacturer is directly related to whether the order can be completed on time. If the manufacturer's production equipment, staffing, capacity scale, etc. are not fully understood, it may face the risk of delayed delivery of orders. Especially during peak seasons or when there are urgent orders, suppliers with insufficient production capacity may not be able to meet the demand, disrupting the purchaser's entire business arrangement.
For example, an event planning company ordered a batch of acrylic rectangular boxes for gift packaging at the event site near a large event. Because the manufacturer's production capacity was not evaluated, the manufacturer could not complete the production before the event, resulting in chaos in the gift packaging at the event site, which seriously affected the smooth progress of the event and the image of the company.
3. Errors in Quotation and Negotiation
The quotation and negotiation with the manufacturer, if not handled properly, will also bring a lot of trouble to the order.
Not understanding that the offer constitutes a hasty signing:
The quotation provided by the manufacturer usually contains multiple components such as material cost, processing cost, design cost (if needed), transportation cost, etc. If you rush into a deal without detailed inquiry and a clear understanding of what constitutes an offer, you are likely to end up with expense disputes or budget overruns at a later stage.
For example, some manufacturers may not be clear about the calculation method of transportation costs in the quotation, or add additional costs in the production process for various reasons, such as material loss fees, expedited fees, etc. Because the purchaser does not understand clearly in advance, it can only accept passively, which leads to the final cost far exceeding the expectation.
There is an enterprise in the order of acrylic rectangle box, that did not carefully ask for the details of the quotation, the results in the process of production were told by the manufacturer due to the rise in material prices, need to pay a high amount of additional material price difference, the enterprise is in a dilemma if you do not pay, you can not continue to produce, if you pay beyond the budget.
Lack of negotiation skills:
Certain strategies and skills are required when negotiating terms such as price, lead time, and quality assurance with the manufacturer. Without these capabilities, it is difficult to obtain favorable conditions for oneself.
For example, in terms of price negotiation, the advantages of bulk purchasing are not mentioned, the bulk discount is strived for, or the delivery time is not reasonably arranged, which may bring additional costs due to early or late delivery.
In the negotiation of quality assurance clauses, the standard of quality acceptance and the treatment method for unqualified products are not clearly specified. Once the quality problem occurs, it is easy to have disputes with the supplier manufacturer.
For example, when a chain retailer ordered a large number of acrylic rectangular boxes, it did not negotiate the delivery date with the supplier. The supplier delivered the goods ahead of schedule, resulting in insufficient storage space in the retailer's warehouse and the need to temporarily rent additional warehouses, increasing operating costs.
4. Negligence in Design and Sample Links
The design and prototyping process plays a crucial role in ensuring that the final product meets expectations, yet it is often overlooked or mishandled.
Design review is not rigorous:
When the manufacturer provides the first draft of the design, the buyer needs to conduct a rigorous review from several aspects.
Focusing on only one aspect of the design while ignoring other important factors such as aesthetics, functionality, and brand identity may result in the finished product not meeting the requirements and requiring rework or even discarding. For example, from an aesthetic point of view, the design pattern, and color matching may not conform to the public aesthetic or the visual style of the brand; From the perspective of function, the opening way and internal structure design of the box may not be conducive to the placement or removal of items. In terms of brand consistency, the size, position, color, etc. of the brand logo may not match the overall brand image.
When a cosmetics company reviewed the design draft of the customized acrylic rectangular box, it only paid attention to whether the appearance color of the box was beautiful, but did not check the printing clarity and position accuracy of the brand logo. As a result, the brand logo on the produced box was ambiguous, which seriously affected the publicity effect of the brand and had to be re-made.
Despise sample making and evaluation:
The sample is an important basis for testing whether the design and production process is feasible. If the production of samples is not required or the samples are not carefully evaluated, the mass production is directly carried out, and the quality, size, process, and other problems may be found after the mass production, resulting in significant losses.
For example, failing to check the dimensional accuracy of the sample may result in a mass-produced box that does not match the size of the item intended to be placed; Not observing the process details of the sample, such as the polish smoothness of the edges and corners, the fineness of the carving, etc., may make the final product look rough and cheap.
There is a craft store in the order of acrylic rectangular box, did not require the production of samples, the results received batch products, there are many burrs on the corners of the box, seriously affecting the display effect of the crafts, and due to the large number, the rework cost is very high, bringing huge economic losses to the store.
5. Insufficient Order and Production Follow-Up
Poor follow-up of the production process after the order is placed also poses a risk to the ordering of custom acrylic rectangular boxes.
The terms of the contract are imperfect:
The contract is an important legal document to protect the rights and interests of both parties, which should clearly specify the specifications of the product, price details, delivery time, quality standards, liability for breach of contract, and other key contents. If the terms of the contract are not perfect, it is difficult to effectively resolve disputes according to the contract when problems occur.
For example, without clearly specified quality standards for products, manufacturers may produce according to their own lower standards; Without liability for breach of contract on delivery time, the manufacturer may delay delivery at will without any liability.
An enterprise does not have clear quality standards in the contract signed with the manufacturer. As a result, the acrylic rectangular box received has obvious scratches and deformation. The enterprise and the manufacturer have no agreement, and the enterprise can only bear the loss by itself because there is no relevant stipulation in the contract.
Lack of production schedule tracking:
After the order is placed, timely tracking of production progress is the key to ensuring on-time delivery. If there is no effective production progress tracking mechanism, it is possible that the situation of late delivery will occur, and the purchaser will not be able to know and take action in time.
For example, problems such as equipment failure, material shortage, and personnel changes may be encountered during the production process, which may be delayed if not tracked in time and ultimately affect the delivery time. In addition, the production process is not tracked, and the quality problems in production cannot be detected in time and required to rectify by the supplier.
For example, when an advertising company ordered acrylic rectangle boxes for advertising campaigns, it did not track the production progress. As a result, it found that the boxes had not been produced until the day before the campaign, which made the advertising campaign unable to proceed normally and caused great reputation and economic losses to the company.
6. Loopholes in Quality Inspection and Acceptance of Goods
Quality inspection and acceptance are the last line of defense in the ordering process, and vulnerabilities can lead to acceptance of substandard products or difficulty in safeguarding rights when problems arise.
No clear quality inspection standard:
When accepting products, there must be clear quality inspection standards and methods, otherwise, it is difficult to judge whether the product is qualified. If these standards are not established with the supplier in advance, there may be a contentious situation where the purchaser considers the product to be substandard while the supplier considers it to be compliant.
For example, for the transparency, hardness, flatness, and other indicators of acrylic sheets, there is no clear quantitative standard, and the two sides may have disagreements. When a technology company accepted a customized acrylic rectangle box, it found that the transparency of the box was not as good as expected. However, because there was no specific standard for transparency in advance, the supplier insisted that the product was qualified, and the two sides were stuck, which affected the normal development of business.
The acceptance process of goods is not standardized:
The acceptance process when receiving goods also needs to be strictly regulated. If you do not carefully check the quantity, check the integrity of the packaging, and sign for the quality by the standard, once the problem is found, the subsequent rights protection will be very difficult.
For example, if the quantity is not checked, there may be a shortage of quantity, and the manufacturer may refuse to replenish the goods based on the signed receipt. Without checking the integrity of the packaging, it may not be possible to identify the responsible party if the product is damaged in transit.
An e-commerce business did not check the packaging when it received the acrylic rectangle box. After signing, it was found that many boxes were damaged. When contacting the manufacturer, the manufacturer refused to assume responsibility for the packaging, and the merchant could only bear the loss himself.
China's Top Custom Acrylic Rectangle Box Manufacturer

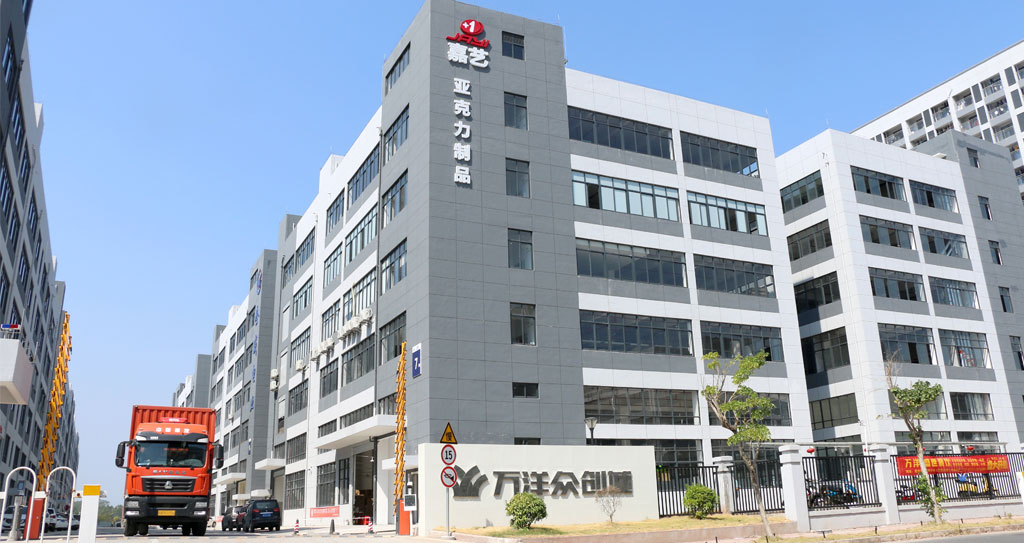
Jayi Acrylic Industry Limited
Jayi, as a leading acrylic manufacturer in China, has a strong presence in the field of custom acrylic boxes.
The factory was established in 2004 and has nearly 20 years of experience in customized production.
The factory has a 10,000-square-meter self-constructed factory area, a 500-square-meter office area, and more than 100 employees.
At present, the factory has several production lines, equipped with laser cutting machines, CNC engraving machines, UV printers, and other professional equipment, more than 90 sets, all processes are completed by the factory itself, and the annual output of all kinds of acrylic rectangle boxes more than 500,000 pieces.
Conclusion
In the process of ordering customized acrylic rectangle boxes, multiple links are involved, and various errors may occur in each link. From the determination of demand, the selection of manufacturers, to the negotiation of quotation, the confirmation of design samples, the follow-up of order production and the acceptance of quality inspection, any small negligence may lead to the final product not meeting the requirements, which will bring economic loss, time delay or reputation damage to enterprises or individuals.
By avoiding these common mistakes and following the correct ordering process and preventive advice, you will be able to order high-quality, customized acrylic rectangular boxes that meet your needs, provide strong support for your commercial activities or personal needs, improve the display effect of your products and brand image, and ensure the smooth development of your business and the complete satisfaction of your personal needs.
More Custom Acrylic Box Cases:
If You Are in business,You May Like:
Post time: Dec-11-2024