Custom Acrylic Products Manufacturer
Get innovative acrylic solutions to help your product and brand stand out. JAYI Acrylic offers the best custom acrylic products for various applications. Our custom china acrylic product designs are creative, functional, and cost-effective to offer the best visual experience. We transform your concepts into acrylic reality, ensuring 100% quality.
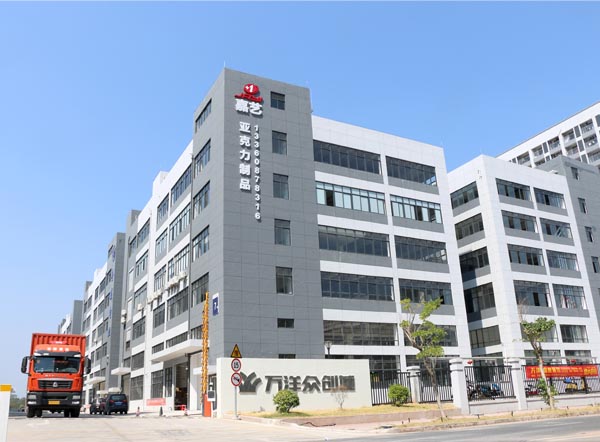
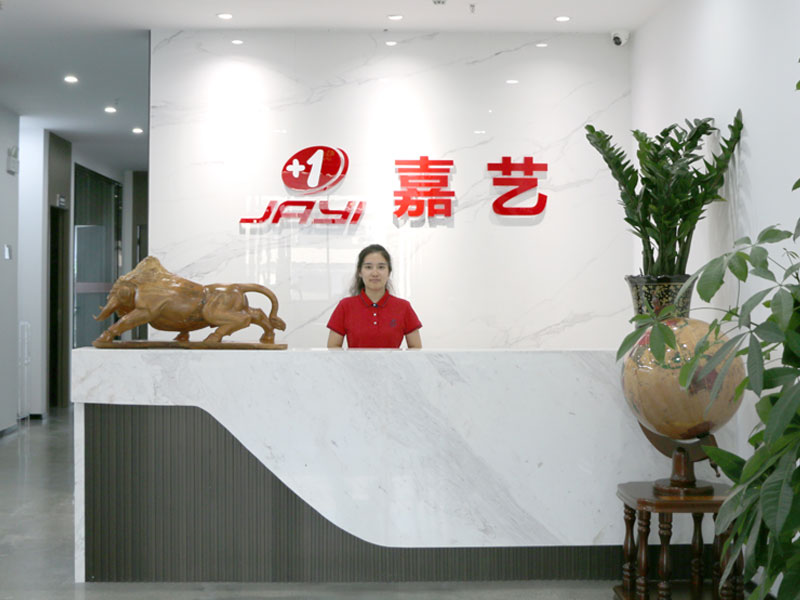
Jayi Acrylic Factory
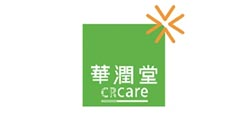
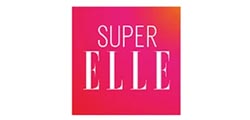
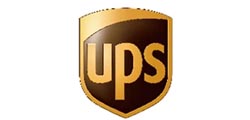
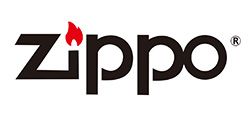
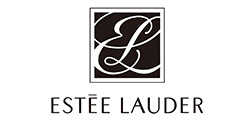
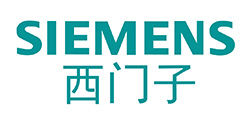
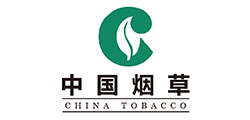
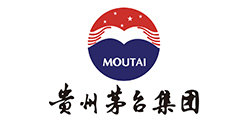
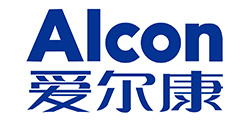
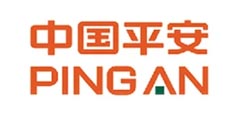
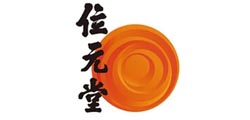
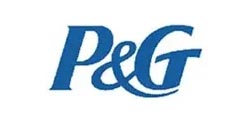
Custom Acrylic Products
Jayi is a leading manufacturer focused on designing and manufacturing high-quality acrylic products. Whether you need customized display products, signage for commercial use, or home decoration, we can provide you with a full range of solutions.
We specialize in custom acrylic product fabrication using state-of-the-art technologies to deliver only the best quality acrylic products.
Custom Acrylic Products Fabrication Services
There are several high-quality custom acrylic product manufacturing and finishing services to enjoy from JAYI Custom Acrylic Manufacturers.
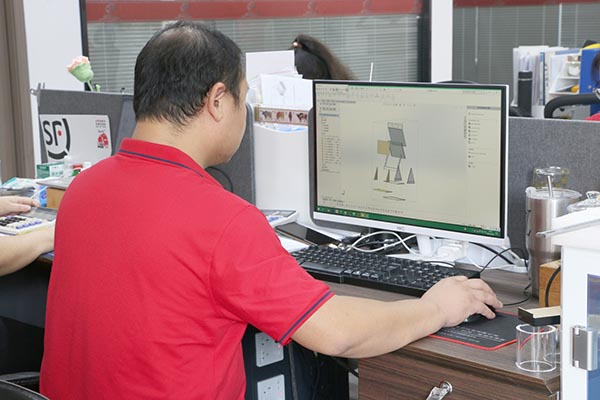
1.Designing
Adequate guidance through each manufacturing stage.
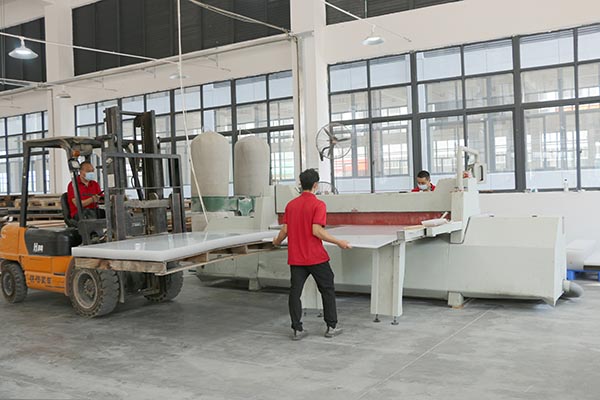
2. Cutting Material
Custom cut-to-size services to meet unique requirements.
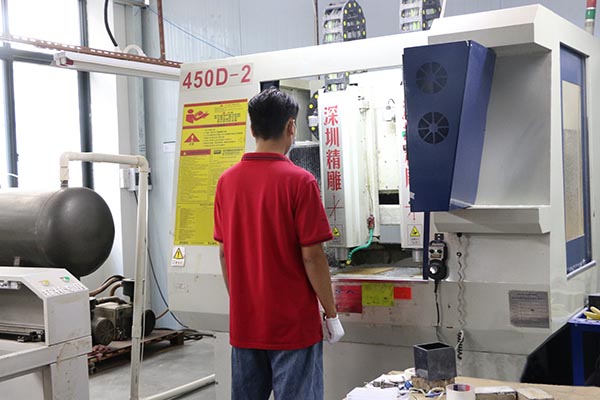
3.CNC Routering
First-class CNC routing services that meet various tolerances.
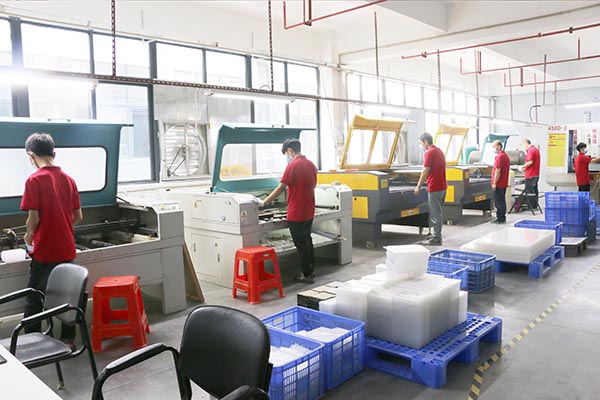
4.Laser Cutting
Precision laser cutting technology to cut out shapes to client satisfaction.
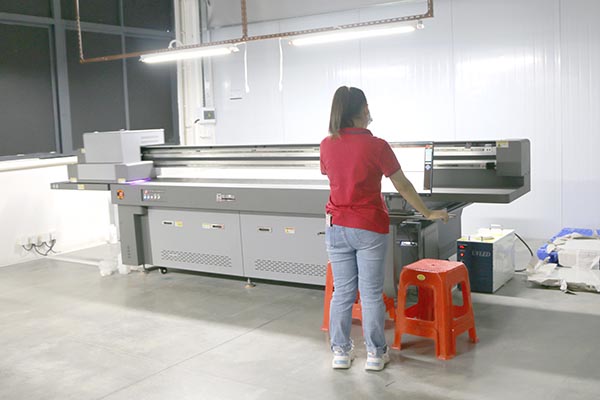
5.UV Printing
Printing for more vibrant color on various surfaces.
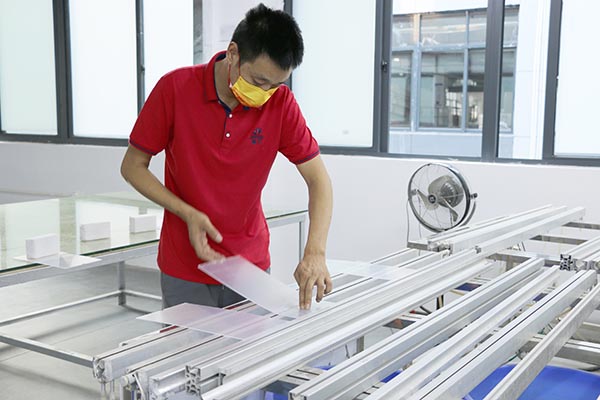
6.Hot Bending Forming
Achieving seamless and unique shapes with specially designed molds for limitless applications.
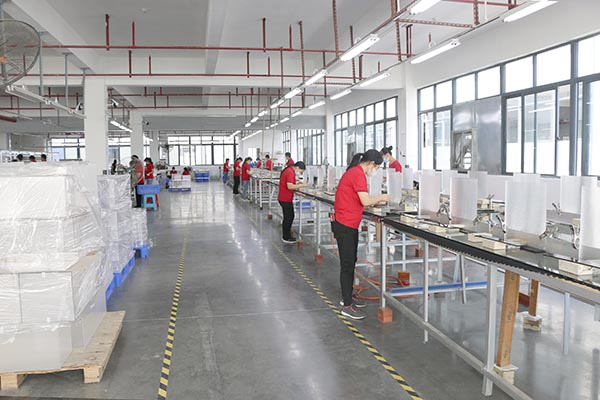
7.Gluing
Achieving seamless and unique shapes with specially designed molds for limitless applications.
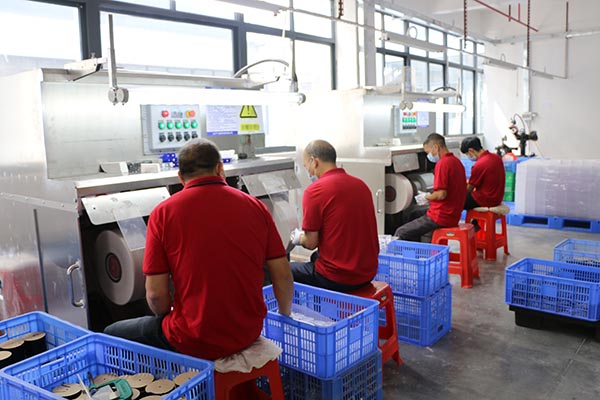
8.Polishing
Smooth and glossy polished finished for aesthetically pleasing products.
Let's start your custom acrylic products project!
Established in 2004, we boast over 19 years of manufacturing with quality processing technology and experienced professionals. We are a professional acrylic products manufacturers and acrylic products suppliers in China.
Why Choose JAYI Acrylic?
From designing to manufacturing and finishing, we combine expertise and advanced equipment to deliver high-quality products. Every custom acrylic product from JAYI Acrylic stands out in appearance, durability, and cost.
9 Steps To Get Your Custom Acrylic Products
Ordering parts from JAYI Acrylic is simple and fast. You can get your desired custom acrylic products following these easy steps:
The first step is very simple, but is very important to ensure customer satisfaction, and it all starts with communication with the customer. When a customer submits a quotation request online or by phone, we will arrange an experienced salesman to follow up the customer's project. During this period, our salesperson often asks the following questions:
What do you want to display?
What are the dimensions of the item?
Need a custom logo on the case?
What level of scratch resistance does the enclosure need?
Do you need a base?
What color and texture do acrylic sheets need?
What is the budget for the purchase?
Through the first step of communication, we have identified the client's customized goals, needs and vision. We then provide this information to our experienced design team, who draws up a custom, to-scale rendering. At the same time, we will calculate the price of the sample. We send the design drawings along with the quotation back to the client for confirmation and any necessary adjustments.
If the customer confirms that there is no problem, they can pay the sample fee (special note: our sample fee can be refunded when you place a large order), of course, we also support free proofing, which depends on whether the customer has strength.
After the customer has paid the sample fee, our professional craftsmen will start. The process and speed of making an acrylic display case depends on the type of product and the base design chosen. Our time to make samples is generally 3-7 days, and each display case is custom-made by hand, which is a big way for us to ensure customer satisfaction.
After the display case sample is made, we will send the sample to the customer for confirmation or confirm it through video. If the customer is not satisfied after seeing the sample, we can proof again to let the customer confirm whether it meets the requirements.
After the customer confirms that the requirements are met, they can sign a formal contract with us. At this time, a 30% deposit needs to be paid first, and the remaining 70% will be paid after the mass production is completed.
The factory arranges production, and the quality inspectors check the quality throughout the process and control each process. At the same time, our salesman will actively and timely report the production progress to the customer. When all the products are produced, the quality of the products is checked again, and they are carefully packaged after no problems.
We take photos of the packaged products and send them to the customer for confirmation, and then notify the customer to pay the balance.
We will contact the designated logistics company to load and transport the goods in the factory, and deliver the goods to you safely and in time.
When the customer receives the sample, we will contact the customer to help the customer deal with the question.